Service Assurance
Our service commitment is not a slogan, an idea or an advertisement, our service commitment is serious. To this end, we have built a large, systematic and standardized service guarantee system to ensure that every link is executed in place and handled with precision.
Closely integrated with Shibang Industrial's business operations, we have formed a large team of installation engineers and specialized them, subdividing them into construction aggregate business installation engineers, ore processing business installation engineers, industrial grinding technology installation engineers and green building materials complete equipment installation engineer. Each field has formed a mix of old, middle and young people to effectively ensure the construction of talent echelon and business employment needs.
Production line inspection
Production line design
Production line construction
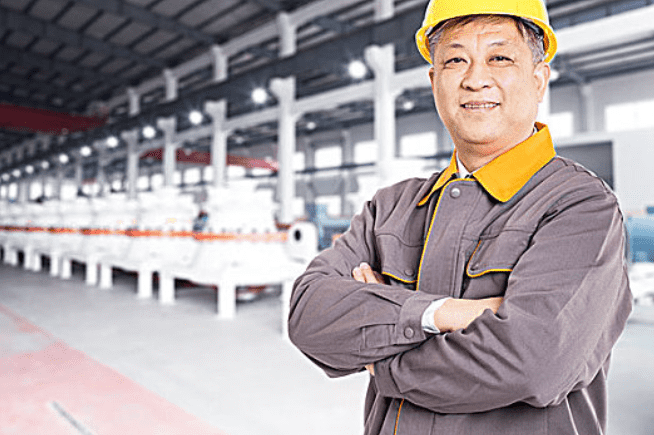

Order Process
Stocking order verification: The merchandiser will verify the model, quantity and accessories of the equipment ordered by the customer in detail according to the sales contract to ensure that the stocking completely matches the order.
Equipment factory quality inspection: After the production system completes the equipment production, the quality inspector strictly checks the records item by item according to the quality inspection details to ensure the quality of each equipment to be installed.
Packing list review: Before the equipment is packed and sent, the order specialist will check the packing list one by one to avoid missing or missing shipments.
Scientific packaging and transportation: In terms of equipment packing and packaging, we use professional packaging and modular solutions to ensure safe and damage-free delivery of equipment.
Modern service standards
During the operation of customer projects, if there is a problem with the production line, customers can make complaints and feedback. We guarantee to complete problem identification and issue solutions within 24 hours, and help domestic/foreign customers solve problems within 3/10 days.